5 Reasons Why Delivery Vehicle Maintenance Needs To Be Part Of Logistics Management
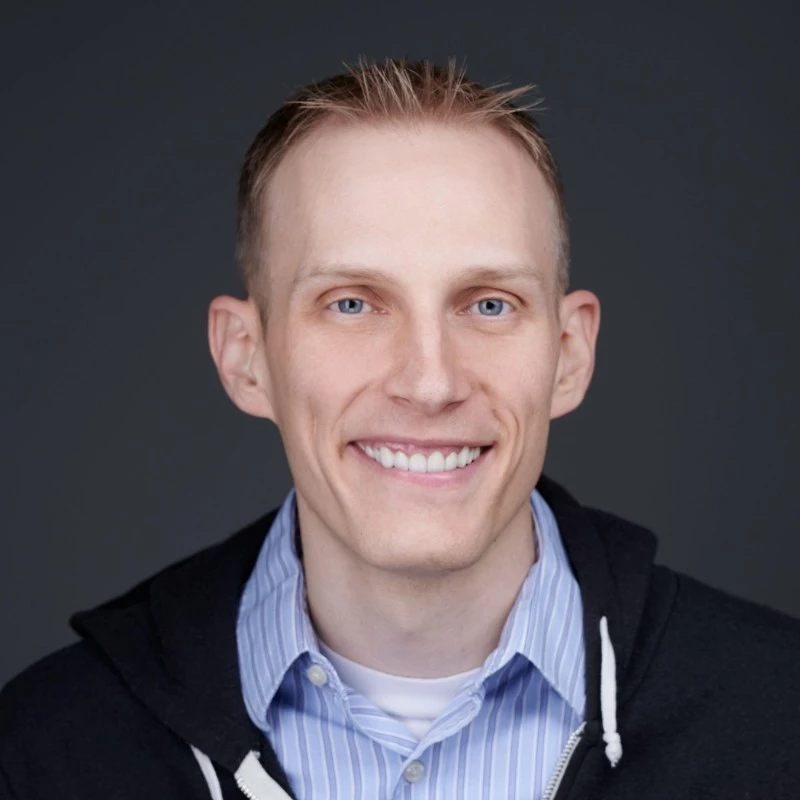
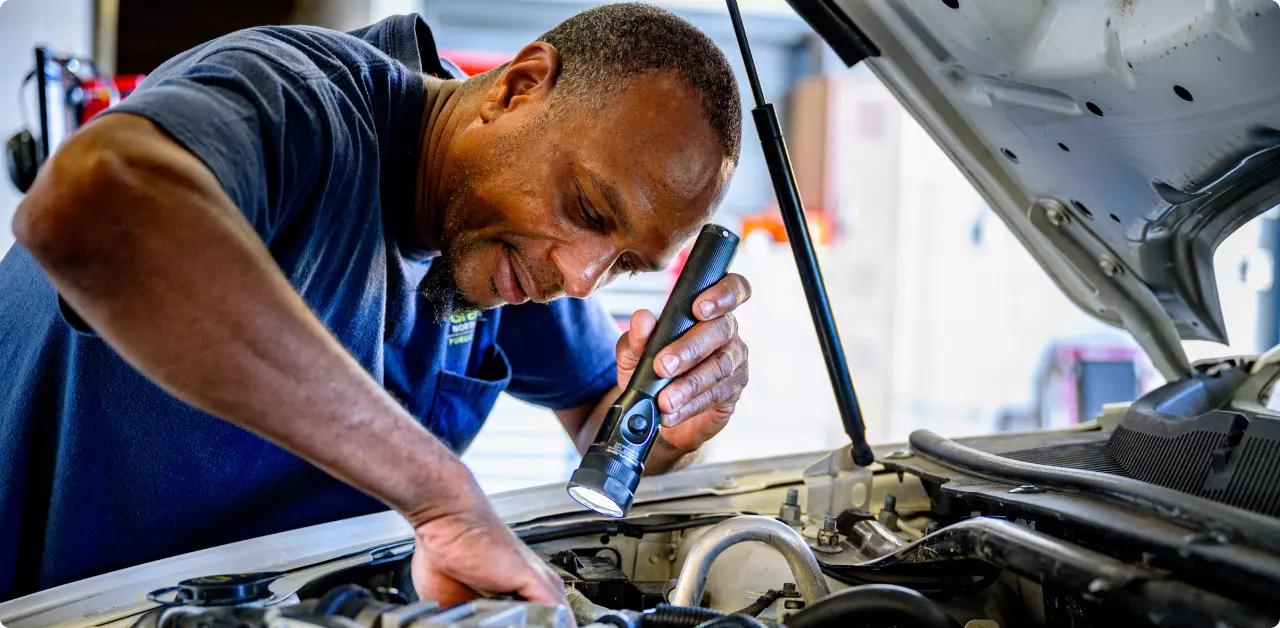
Prioritizing delivery vehicle maintenance streamlines the work of any logistics company. It improves the availability, reliability, and durability of delivery vehicles. By doing so, it also helps with faster and more predictable last-mile deliveries, lowers costs, improves customer satisfaction, and boosts revenue.
Logistics management companies can use different metrics to monitor their delivery fleet maintenance programs. They use indicators like fuel consumption, vehicle availability (breakdown frequency), fleet productivity (are deliveries within the recommended timelines?), and total maintenance costs.
They can use several maintenance strategies depending on the size of the fleet, their maintenance goals, and the available budgets. These strategies include:
- Corrective maintenance: Fixing problems after a delivery vehicle breaks down.
- Preventive maintenance: Regularly scheduled maintenance based on manufacturer recommendations and each vehicle’s operating history.
- Predictive maintenance: Using data from vehicle sensors to track performance metrics, identify changes, and predict when failures are likely to happen.
Why delivery vehicle maintenance matters
Logistics management companies should develop a robust delivery vehicle maintenance program to make their operation seamless. This also helps with adequate asset care and strategically scaling last-mile delivery operations without additional vehicles.
Here is why proper delivery fleet maintenance matters.
1. Improved vehicle availability and extended lifespan
Delivery vehicles are the backbone of routine logistics operations. As such, they must be available on demand. Frequent fleet failures lead to:
- missed delivery targets
- lower customer satisfaction
- premature asset retirement
- increased maintenance costs.
A reliable delivery fleet maintenance program helps define various inspection and preventive maintenance intervals.
Maintenance technicians take care of lubrication, engine oil changes, and inspect mechanical and electrical components. Planned maintenance can identify problems that can disturb the performance and availability of the delivery fleet. Technicians can fix these issues before they interrupt normal operations. This ensures that all delivery assets are available for use.
Logistics management companies depend on regular maintenance to identify and replace worn-out vehicle components. These components, however small, have a significant impact on the operation of a delivery vehicle. When worn-out parts fail, the damage can extend to other critical vehicle parts.
For example, disregarding signs of wear and tear on the timing belt or chain can cause irreversible engine damage. This can lead to a complete engine overhaul, removing the vehicle from operation.
Scheduled maintenance ensures the company sets aside time to inspect, identify and replace components showing signs of failure. This prevents sudden asset failures and prolongs the lives of delivery vehicles. It also means companies can get high returns on investment throughout their lifetime.
2. Enhanced fuel efficiency
Delivery vehicles get poor fuel mileage due to:
- deflated tires
- clogged air filters (blocked or dirty air cleaners restrict airflow to the engine)
- dirty fuel cleaning system
- worn-out engine components
- untuned engine.
Poor fuel economy is bad for business. It implies the company spends more on fuel, reducing their profit margins and sometimes causing financial deficits.
Logistics management companies can control their delivery fleets’ fuel consumption through well-scheduled, data-driven maintenance practices. They should train delivery drivers to perform pre-trip checks and monitor vehicle conditions. They can check tire inflation to minimize rolling resistance, which improves fuel efficiency. All these checks can also help to improve driver safety while on the road.
Regular preventive maintenance goes above simple mpg (miles per gallon) monitoring. It also takes vehicle usage patterns and miles covered into account. Delivery vehicles that drive long distances on dirty (dusty roads) need air cleaners changes earlier than short-haul, last-mile delivery service vehicles.
A good maintenance program includes engine tuning, fuel system inspection, and cleaning intervals. These are labor-intensive and time-consuming procedures. Companies should schedule such interventions for periods with low delivery fleet demand.
Maintenance technicians should also replace worn-out parts which cause the engine to work harder. This includes:
- worn-out spark plugs
- defective oxygen sensors
- aging engine oil.
Replace engine oils with alternatives like synthetic oils, which reduce friction among internal engine components. This significantly increases fuel economy.
3. Better compliance
Delivery vehicles must comply with various safety, environmental, and local or state authority regulations. These vehicles should meet the minimum safety requirements set by:
- Federal Vehicle Safety Standards (FMVSS) — safety requirements related to braking, lightning, and crashworthiness
- Environmental Protection Agency (EPA) — requirements related to emission standards
- Department of Transport
Non-compliance usually leads to fines. Since these can go up to several hundred or thousands of dollars, they eat into the slim profit margins in the industry.
Delivery vehicle maintenance keeps all components in good working condition. It improves compliance standards with various statutory requirements.
For instance, technicians can use the maintenance intervals to replace worn-out parts, repair defective lighting systems and fix multiple problems related to compliance. They can also fix fuel system issues and inspect emission control devices — like the catalytic converters — to ensure emissions are within the recommended levels.
Adequate emission control helps logistics maintenance companies comply with environmental protection policies, reduce their carbon footprints, and enhance their reputation as environmentally responsible companies. It also optimizes energy and fuel efficiency, resulting in significant cost savings.
Properly-maintained vehicles are less likely to break down during operations. Maintenance improves delivery fleet reliability and minimizes incidents that could result in the violation of numerous DOT regulations.
4. Enhanced safety features
Logistics management companies are obliged to:
- observe several safety measures on the road
- ensure all employees work in safe and secure environments
- safeguard the lives of other road users.
Poorly-maintained vehicles can break down without notice. This endangers the lives of delivery drivers and other road users. Some delivery vehicles transport hazardous materials, while others carry specialized equipment — like refrigerators for food delivery or liftgates for box trucks — whose failures can harm operators and damage goods. Drivers and operators should not strain when working with the delivery fleet.
Regular delivery fleet maintenance and inspection are integral for optimizing the safety of the employees, the environment, and other road users. Technicians identify several defects and promptly repair them before they cause accidents or injuries.
The company also performs preventive maintenance activities (oil changes, frequent lubrication, transmission fluid changes, tire rotations…) to minimize the risk of vehicle failures — they increase the probability of accidents and workplace injuries.
5. Increased revenues
The profitability of a logistics management company depends on the number of orders it picks and successfully delivers. Maximizing delivery fleet maintenance means the company can achieve and surpass its targets, and organically grow its revenues.
These companies evaluate market dynamics and use previous maintenance and operations records to predict future demand, and develop long-term revenue generation plans. Such planning is ineffective if the available delivery vehicles break down frequently or if the company doesn’t have a functioning maintenance program.
Dependable maintenance programs reduce delivery fleet downtime — the amount of time the delivery fleet is out of service is predictable. It means the company meets different client expectations, opening up opportunities for repeat businesses and referrals. The company also avoids costly delivery vehicle repairs by handling minor issues before they escalate.
Over time, the company gets a clear picture of asset-specific maintenance requirements and the associated costs. They use this information to optimize maintenance budgets and promote efficient asset utilization for lower fuel consumption and an extended lifespan.
Establishing a delivery vehicle maintenance plan
Delivery vehicle maintenance may sound simple to implement on paper. However, establishing a maintenance plan takes time and requires various resources.
Here are a few tips logistics management companies can use when developing a maintenance plan — one that is scalable as the business expands.
Digitize vehicle maintenance planning
Companies can establish effective maintenance programs and allocate adequate funds but fail to implement preventive and corrective measures due to inconsistency in maintenance planning. These excessive workloads can sometimes cause companies to defer critical maintenance tasks.
These companies require a centralized maintenance planning solution that generates timely alerts and provides a centralized dashboard to manage the maintenance of multiple assets.
Companies can invest in a customized Computerized Maintenance Management System (CMMS) to automate delivery vehicle maintenance planning and build a data-driven asset management program. A CMMS program allows logistics management companies to:
- monitor maintenance metrics like the Mean Time Between Failures (MTBF) and the Mean Time To Repair (MTTR)
- upload vehicle-specific maintenance requirements
- store maintenance histories
- store and update troubleshooting and repair manuals
- get insights into maintenance budgets.
This improves the visibility of maintenance operations and provides companies with enough data to optimize maintenance schedules, enhance the accuracy of maintenance tasks, and control maintenance budgets.
For more precise delivery vehicle maintenance, companies can use advanced asset maintenance technology like sensor-based predictive maintenance. Shifting from manual to digital maintenance scheduling reduces planning errors and improves data collection from different facets of logistics management. This data is beneficial for designing training programs for drivers, in-house maintenance teams, and other employees in the supply chain.
Streamline vendor management
A small logistics management company relies heavily on vendors to manage delivery vehicle maintenance stocks. Companies engage these vendors whenever maintenance, repairs and operations (MRO) supplies are required.
They supply the parts in time for scheduled and emergency delivery vehicle maintenance. Delayed vendor deliveries jeopardize maintenance operations, leading to deferred maintenance tasks and inadequate repairs — causing costlier fleet breakdowns.
Logistics management companies should find reliable vendors within their areas of operations. Verify if the vendor stocks repair parts relevant to vehicle brands in your fleet.
The company can enter into agreements with MRO vendors and agree on specific payment methods, delivery timelines, and applicable warranties. Such measures ensure every party plays its part in timely, affordable, and accurate delivery fleet maintenance.
Prioritize inspections and repairs
Logistics management companies need to categorize and prioritize fleet inspections and repairs when developing a maintenance program.
Drivers of different delivery vehicles — cargo vans, delivery vans, delivery trucks, light-duty trucks, even pickup trucks and electric delivery vehicles — can report multiple issues at once. That does not mean grounding all the affected assets there and then — it would leave the company with a limited delivery capacity.
The company assigns risk scores to various delivery fleet defects and prioritizes the repair of critical defects limiting the performance of an asset. The company can invest in operator and driver training and equip them with adequate technical skills to perform simple tasks like cleaning the cargo space, tire inflation, checking coolant levels, filling work request forms, or inspecting windscreen wipers or rear doors. Drivers and operators can complete these tasks in a few minutes.
However, more complex maintenance tasks like engine overhauls or transmission system repairs require several hours to complete, and demand approval from several decision-makers in the company. All-electric vehicles also fall into the category of complex maintenance.
The maintenance program should outline which maintenance task comes first and how long each activity should take — provided all maintenance resources are available — to ensure minimal disruptions to delivery targets. Maintenance prioritization also influences the allocation and utilization of maintenance budgets.
Final words
Delivery vehicle maintenance is crucial for any logistics management company with a long-term plan to remain competitive and adopt innovative long-distance or last-mile delivery initiatives.
Proper delivery fleet maintenance boosts the reliability and durability of delivery vehicles for better customer satisfaction, predictable budgeting and planning, longer fleet lifespan and increased revenues.
Companies can achieve better delivery vehicle maintenance by:
- implementing relevant digital technology for data-driven maintenance initiatives
- more accurate maintenance planning
- better access to mission-critical technical information.
Continuously improve delivery vehicle management programs as the size and type of the fleet expands, and as the company integrates advanced digital technology into routine operations.
Frequently Asked Questions
Related articles
Liked this article? See below for more recommended reading!
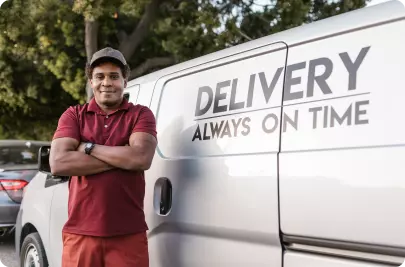
What is Delivery Management? A Guide to the 6 Pillars
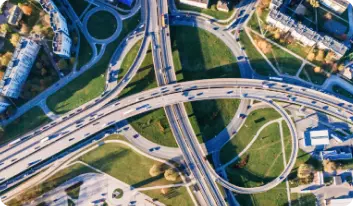
What is Vehicle Fleet Management?
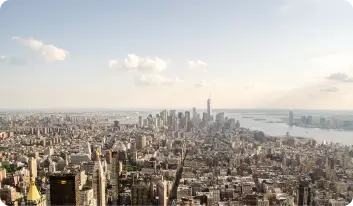