Route Optimization: Transforming Last-Mile Delivery Operations
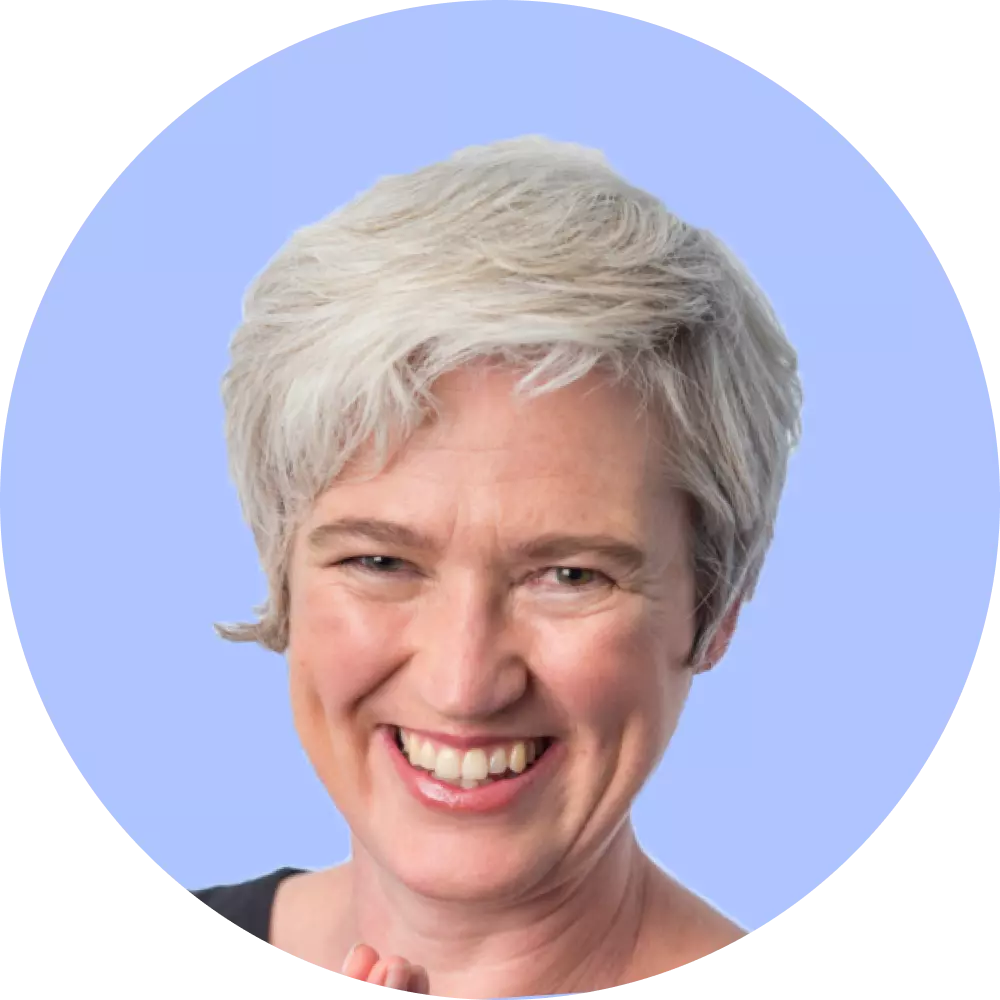
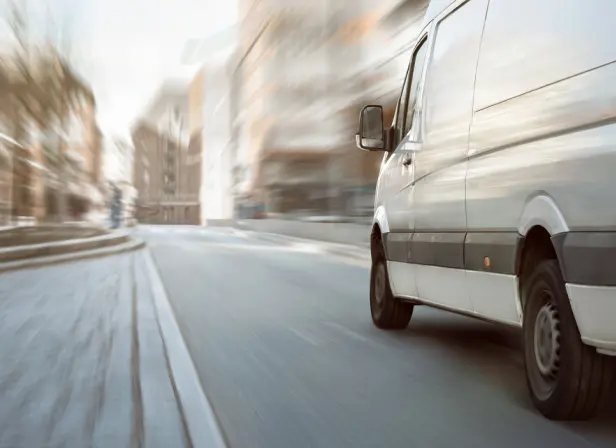
- The last mile of the supply chain is expensive for businesses and harmful to the environment.
- Last mile delivery lacks economies of scale because there are so many single-item deliveries.
- Fuel, labor, and vehicle costs are major components of the overall cost. Other components include administration, customer communications, failed deliveries and returns (reverse logistics).
- Greenhouse gas and particulate emissions, along with packaging waste, are the major environmental problems with the last mile.
- Last mile delivery route optimization is the single most important strategy for reducing costs.
Optimizing last-mile delivery operations is critical for delivery companies of all sizes, from the tiniest startup to the biggest multinational firm.
Why? Because even though the last mile typically involves shorter distances than any other part of the supply chain, it’s also the most expensive, accounting for more than 40% of total shipping costs. That means a massive impact on profitability — so any last mile delivery strategy that can bring the costs down will have an outside effect. This is especially true for small businesses that serve only local customers, and so are taking on a very expensive part of the delivery process.
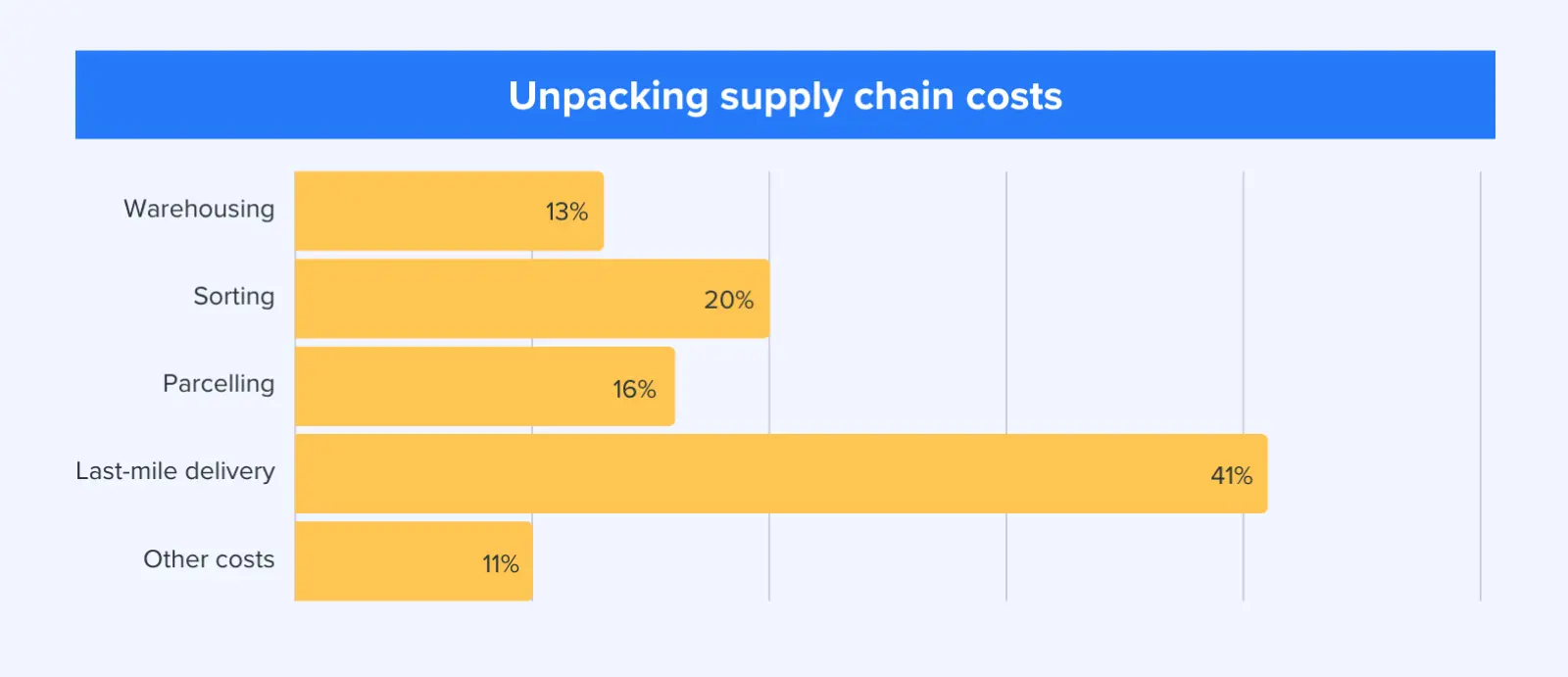
The last mile delivery market is predicted to grow at nearly 7% a year between 2022 and 2030. With the transportation sector accounting for just over 20% of global greenhouse gas emissions, that means optimizing the mile is important for environmental reasons as well.
In this article we’ll look in more detail at the problems with last-mile delivery. We’ll also look at a range of solutions to make last mile logistics better for the bottom line, more convenient and less harmful to the environment.
Last mile delivery challenges
A. The last mile is expensive
The single biggest last mile delivery challenge facing businesses across the world is cost. Delivering directly to a customer’s doorstep is expensive, and most of the time the costs aren’t covered by the customer.
There are several components to this cost:
1. Single-item deliveries
Unlike large-scale shipping and distribution, which usually involve large volumes, last mile delivery means transporting lots of small packages to single destinations. Yet the cost of delivering one box of apples to a home is pretty much the same as the cost of delivering a hundred boxes to a store. The last mile doesn’t benefit from any economies of scale.
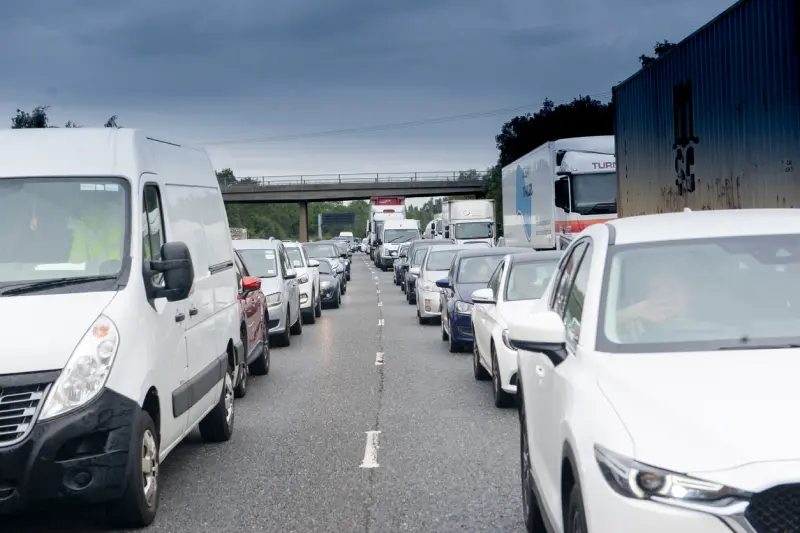
2. Fuel
Most last-mile deliveries are in urban areas, and stop-start city driving and traffic congestion are a worst-case scenario for high fuel consumption. The price of gas is a given, so the only way to reduce this cost is to drive shorter distances by using last-mile delivery route optimization.
3. Labor
Last-mile delivery is labor-intensive, with the potential for lots of overtime. Staff turnover tends to be high, leading to higher costs for hiring, training and managing new drivers.
4. Vehicles
Delivery vehicle costs include maintenance, repairs, and insurance, as well as the costs of buying or leasing the vehicles. Specialized vehicles like refrigerated trucks cost more; and regulatory requirements like emissions standards can add to the expense.
5. Administration
Managing the delivery process involves a lot of back-office work in scheduling, route planning, dispatch management, and customer service.
6. Customer communication
Dealing with “where is my order?” calls is time-consuming, especially if businesses don’t have real-time visibility into their delivery processes. In fact, 28% of retailers report this as one of their top six cost concerns. It also makes for a poor delivery experience and low customer satisfaction.
Customer expectations for ever-faster deliveries are a big factor in last-mile logistics as well, but these expectations can be unrealistic. Small businesses may be able to benefit by pushing back, with clear communication about the costs (including environmental costs) of high-speed delivery that helps to convince customers they can wait a day or two after all.
7. Failed deliveries
Many deliveries can’t be completed on time because the customer is not home, the driver can’t find the address, or the driver can’t get access to the building. Every failed delivery needs to be rescheduled or sometimes refunded, and the costs add up fast.
8. Reverse logistics
Handling returns, refunds and failed deliveries is a big issue for e-commerce businesses. More than 70% of U.S. consumers have returned an online purchase at least one, and in 2023 alone consumers returned merchandise worth a massive $744 billion.
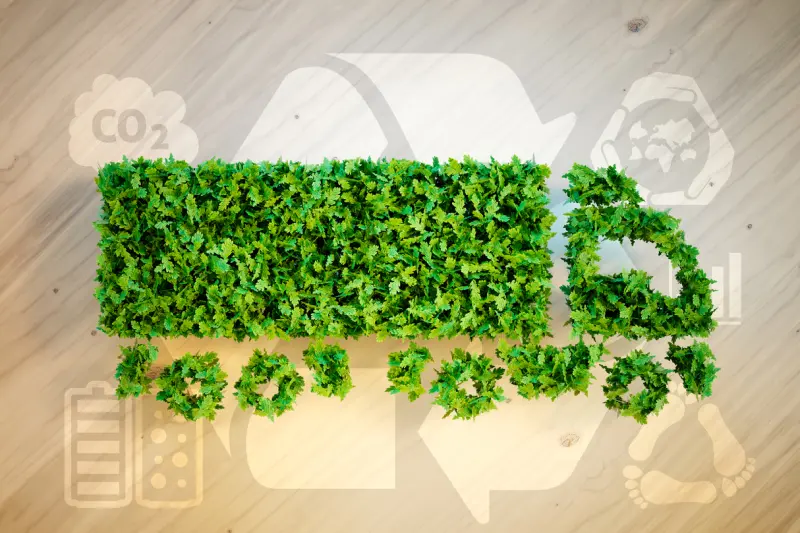
To sum up, the main contributors to the high cost of last-mile delivery come down to:
- More time on the road per delivery
- More distance driven per delivery
But the cost isn’t the only problem with the last mile. Let’s look at the other significant problem:
B. Last-mile delivery is bad for the environment
For many of the same reasons it’s expensive, the final mile in the delivery process also comes with a lot of problems for the environment:
1. Greenhouse gas and particulate emissions
Even though the market for electric delivery vehicles is growing fast, they’re still a tiny proportion of the total — and all those heavy vehicles on the road cause a lot of pollution. Even electric vehicles won’t entirely solve the problem, because the particles shed by tyres are a massive problem all on their own.
2. Packaging waste
Demand for sustainable packaging is also growing, but again we’re still in the beginning stages. And meanwhile, online shopping generates nearly five times as much waste as offline shopping. The world is producing twice as much plastic waste as we did two decades ago, and much of it is ending up in rivers, oceans and farmland — with dire consequences for our health.
So what is to be done? In the next section we’ll look at strategies for optimizing the last mile to reduce these negative impacts.
5 strategies for last-mile optimization
There are several ways to optimize the final leg of the supply chain, leading to reduced operational costs and environmental impacts. Here are five of the most effective:
1. Optimize routes
Distance driven per delivery is one of the key problems in the last mile, contributing to both cost and environmental impacts. Route optimization is the most effective way to shorten that distance — which is one reason 72% of global enterprises are looking at better planning, including route optimization, as one of their supply chain optimization strategies.
Route optimization software uses AI and advanced algorithms to create the most efficient routes, considering data points like distance, time, location, driver capacity, and traffic. Optimized routes can be adjusted in real time if needed, ensuring maximum operational efficiency.
Delivery management software that includes route optimization usually comes with other useful functionality that results in better customer experience, including:
- Automated customer notifications alerting recipients to the expected time of arrival (ETA), and confirming when the delivery has been completed.
- Proof of delivery features like photographs and signatures.
- The ability to offer preset delivery windows. In one study 73% of consumers said a convenient delivery time window is more important than fast delivery.
- Delivery schedule automation, including planning around driver shifts and availability.
- Real-time tracking links for customers. This adds a level of predictability and control that helps with higher customer satisfaction.

2. Offer a variety of delivery methods
Last mile delivery doesn’t have to involve a trip to the customer’s doorstep for every package. Online retailers can increase their efficiency by offering alternative delivery methods at a variety of price points, for example:
- Buy online, pick-up in store (BOPIS): Customers complete their purchase online, then pick up their order in person at a time that suits them. This eliminates delivery costs entirely! It can also increase foot traffic in stores, potentially leading to additional sales.
- Slower delivery: Not all customers need or want next-day or same-day delivery. Offering a slower, but cheaper, delivery option can help reduce costs, since delaying deliveries means they can be grouped for more efficient routing. And 86% of consumers are willing to accept slower delivery times if there’s a sustainability benefit.
- Delivery to a parcel locker: Parcel lockers are secure storage spaces where customers can pick up their packages at their convenience. They are becoming more popular, and can be found in apartment buildings, office blocks and even at retail locations. This can increase the number of deliveries per stop, and also eliminates the need for multiple delivery attempts when customers are not home.
3. Consider alternative delivery vehicles
Route optimization reduces both miles driven and fuel consumption. But another to cut fuel costs is to use more efficient vehicles like:
- Electric delivery vans
- Scooters
- Bikes and electric bikes
In dense cities with lots of traffic jams, electric bikes can often be both a more cost-effective and a faster way to make last-mile deliveries.
4. Explore partnerships and collaborations
Partnerships are another way to increase the number of products in each package, and thus the profitability of each dropoff. For example, Terra Firma Farm in Connecticut includes produce from several other local businesses in their online shop, making for bigger orders. Another strategy is to drop off a number of orders at a central distribution hub like a retail store or community center.
5. Optimize for sustainability
We’ve already mentioned route optimization as one growing trend towards reduced vehicle miles for greater sustainability. There is plenty of work to do to optimize packaging as well:
- If you have regular customers, consider offering reusable packaging. Vancouver florist Bear’s Blooms, for example, delivers flowers in cardboard boxes that customers can leave out for collection on the next delivery day. That means the florist can re-use each box several times — and makes customer more likely to sign up for a regular subscription rather than a once-off delivery.
- Some consumers are prepared to pay extra for a white glove delivery service that includes unpacking purchases and removing all the packaging.
- More suppliers are offering recyclable and even compostable packaging options.
By implementing these strategies to optimize the last mile delivery process, businesses can significantly reduce their delivery costs and increase their overall profitability.
Frequently Asked Questions
Related articles
Liked this article? See below for more recommended reading!
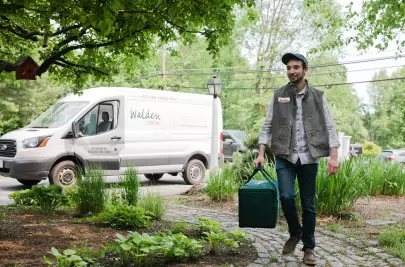
Walden Local Expands Home Delivery With Intelligent Route Optimization
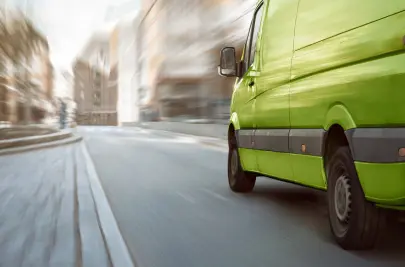
Best Last Mile Delivery Software 2025: Reviews & Guide
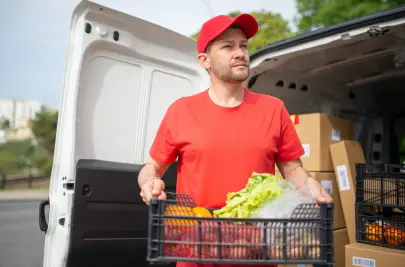